
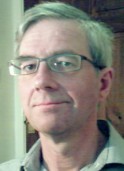
Wheel Bolts
I remember my dad changing wheels on his car. The tool provided for the purpose was a dual-use one. It was a large cranked rod with a socket on one end and a bayonet-style spigot on the other. The socket was for undoing wheel nuts and the spigot was for cranking the engine when the starter wasn't working. He would always start by jumping up and down on this tool to loosen the nuts and finish by doing the same to tighten them.
It never occurred to me this was not the correct procedure. It was what everyone I knew did in those days, until, that is, I fitted a wheel in the presence of a vehicle engineering technician when I worked at a college in my twenties. He was horrified.
“If the manufacturer thought the bolts needed to be tighter than you can get them with your hands,” he said, “They’d have given you a longer spanner.”
With my current car and the arrival of the Internet, I know the manufacturer’s recommended torque wrench settings and, using that most useful tool, I can tighten my wheel bolts with confidence knowing they are tightened to the right amount according to the official instructions. It’s nowhere near as tight as most people would imagine. Obviously, they do have to be tight enough to do their job without any risk of them working loose, but once that’s achieved there’s little to be gained by tightening them further.
There is, in fact, something to be lost. First of all, overtightened bolts can be very difficult to undo, and secondly, extreme overtightening could cause damage or increase the risk of a wheel falling off! Consider what part of the bolt is actually holding it, and therefore what it secures, in place. It is not the thick chunky core of the bolt. Rather it is that thin strip of metal round its circumference normally known as the thread. It is the thread which has to handle the stresses as the bolt is pulled around. It is the thread which must not break off if the bolt is to stay in place. It is the thread which will be pulled on as the bolt is tightened, and it is the thread which will be subject to sheer stresses as its spiral is pushed sideways by continuing to turn the head after it is tight. That is not the only source of such stress. As the car takes corners its mass must be forced into a new direction. It is the wheels which must do that forcing as the car is steered, and it is the bolts and their threads which must connect that force to the brake drums or discs and, through the bearings and suspension, to the whole car. Moreover, as the wheels are also rotating that force is cyclical on each bolt in turn. If the thread is already stressed near its breaking point that extra pulsing stress could just be too much. If the thread is stripped the bolt will cease to work and the wheel will part company with the car. Of course, such an event is, fortunately, very rare, but overtightening the bolt would increase the risk.
However, even garage mechanics seem not to understand this. Unless you specifically ask them to use a torque wrench they will generally just tighten the wheels as far as their power tool will go, making it almost impossible for the customer to get the wheel off in the event of a puncture or similar event. They sometimes blame rust, arguing that the correctly tightened bolts have swollen and thus tightened themselves further. I can’t deny that happens, but I suspect it’s more of an excuse than a reason in many cases.
I came across this problem the other day. I’ve seen too many examples of jacking damage to entrust removing wheels to the average tyre fitter. I much prefer to remove a wheel with a tyre needing replacing from the car myself and then take it into the shop to have the new one fitted. Then I can put it in my chosen position on the front of the car where tyres wear most and move the tyres round to get the ones with most tread on the front and the others on the back or as the spare. (My car still has a proper spare.) However, this relies on being able to undo the bolts, and all efforts failed.
At this point I suppose I should mention another fallacy regarding wheel bolts. Most people seem to assume the best way to apply maximum force to a stubborn bolt or nut is to push downwards with their weight. This is not true and moreover, the more weight I put on the spanner the less weight I put on my feet. In the worst case I could finish up balancing on the spanner with my feet off the ground, and that’s not a stable position. It can twist the spanner off the nut causing bruised knuckles and damage to the mating surfaces of the spanner and nut.
However, if we reflect that in order to walk up stairs or leap into the air our legs have to be able to exert a force greater than our weight, we should realise we can actually apply more upward force on a spanner than downward force, simply by starting in a squat and standing up. This also pushes our feet harder onto the ground and ensures we won’t overbalance. It is important to be aware of stresses on our back, of course, to avoid crushing a disc.
It was with this knowledge I tried to loosen my wheel bolts to remove a tyre which is beginning to leak. At nearly fourteen years old it either has a slow puncture or has perished. The problem was that however hard I pulled, the bolts just would not budge. I had to give up.
Today I reflected on that and came up with an unorthodox and not to be recommended plan. However, I judged it worth a try if I took great care. I realised that although I could not lift the spanner hard enough, the car came with a tool which, provided it didn’t slip out of position, could. Could I put the bolt to be slackened at the bottom of the wheel and position the spanner horizontally? Yes, I could do that, and if I put the jack under the end of the spanner and wound it up, how far would it have to lift before the bolt started to unscrew? It worked. It loosened the bolts just enough that I could now just about turn them. After each bolt I took the handbrake off and rolled the car backwards or forwards to position the next bolt and repeat the process. Soon I was using the jack for its proper purpose and I changed the wheel with no further trouble. Once I had the car back on the ground and the spare tyre inflated to the right pressure, I used my torque wrench the finish the job.
I can’t recommend anyone else do what I did. If something broke the forces released might cause injury. However, I did finally manage to get my job done, and nothing did break, so I got away with it.
Now I can get the tyre replaced and let’s hope the other wheels are not similarly too tight.